How Dallas Johnson Greenhouses Is Simplifying Shipping
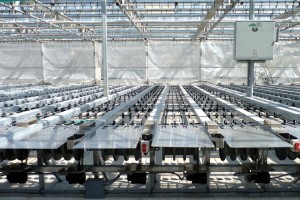
Dallas Johnson Greenhouses can load as many as 150 skus on its new shipping system at a time
Two years ago, Dallas Johnson Greenhouses, a 61-acre operation in Council Bluffs, Iowa, and No. 21 of Greenhouse Grower’s Top 100 Growers, was struggling to get its orders out. With its range of potted annuals, there were so many skus that it was impossible to get enough carts into the shipping greenhouse, and the crew couldn’t get orders processed fast enough. As a result, the operation was consistently pulling orders until midnight every night during the busy shipping season, says President and CEO Todd Johnson.
So Johnson got together with Arie Van Wingerden at Cherry Creek Systems to discuss his problem, and what they came up with has changed everything, Johnson says.
Inside one of Dallas Johnson Greenhouses’ existing structures, the team installed a shipping system made with Echo-Veyors, the popular cable conveyor system designed by Cherry Creek Systems. The system was placed right in the front of the greenhouse, off the shipping area, so plants stay healthy with enough light and air that they can stay on the shipping line for a couple of days if needed. The open roof, Rough Brothers greenhouse stands just over an acre, providing the shipping capacity that wasn’t available before, when the operation brought everything up on carts, and then transferred plants from the smaller carts that were used internally to the larger carts for shipping.
“I envisioned when we put the system in place that we’d have a big staging area for the orders,” Johnson says. “Well, the plants flower so precisely and so evenly coming out of the three different pulling areas we have that they’re going right into the trucks, so we never even needed that.”
Working Out The Kinks
Designed last November, the system took about 2 1/2 months to put together, and was put into initial operation in early March 2015.
Each of the belts is about 22 inches wide by 45 feet long, and there are 330 belts, which can each hold about 75 trays.
“We’ll have as many as 150 skus on it at a time,” Johnson says. “It’s about 396 feet from the start of it to the end, so in that space, we can pull all the different skus in just one area.”
Going through its first season with the shipping system in place in spring 2015, Johnson was able to see what it was capable of, and note any kinks that needed to be worked out. For instance, some of the trays didn’t fit on the cable system correctly, so Johnson had to change the trays it was using to fit the system.
“It goes all the way down to the plastics,” he says. “Everything has to work together in concert, or else the whole system doesn’t work right.”
Realizing A Whole New Level Of Efficiency
To streamline order processing, the operation has a night crew load the system, based on orders for the following day.
The next morning, orders are processed in significantly less time, generally ending around 6:30 p.m., Johnson says. On a normal spring day during the spring season, orders were pulled, processed and loaded on trucks until sometimes midnight and even 1 a.m. Last spring, the latest the shipping crew worked was 8:30 p.m.
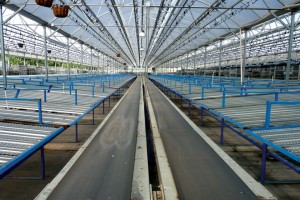
The new Echo-Veyor has significantly reduced the amount of time the team at Dallas Johnson Greenhouses was spending pulling orders and shipping in the spring
“It does two things: it reduces your cost for shipping, not as much as one might think, but it improves quality and also makes it more efficient for us with precise pulling,” Johnson says. “Every time we pull the orders correctly, there are fewer substitutions and more effective labor. And that’s the biggest one, with being how increasingly difficult it is to find labor these days. The system made their jobs easier, and it was very easy to retain employees in that area.”
The Echo-Veyors feature watering booms, allowing plants to be watered to keep them at peak health through the shipping process, Johnson says.
“Generally we water every three days with the booms, and then the two days between the boom watering, we watch the plants and water by hand if needed,” he says. “The night crew sets the booms to water at 3 a.m., so when we start shipping in the morning, everything is watered. We found out if we ran the booms every day, some of the stuff that sat on there started growing again, which we didn’t want it to do, so we had to manage it a little more closely.”
New System Provides Unexpected, Indirect Benefits
Quality of shipments has improved, as well, and plants are selling better at retail because of it, Johnson says. Dallas Johnson Greenhouses serves big box stores, as well as local grocery stores and independent garden centers.
“Quality has improved because before, we used all of our resources just to get the material out the door,” he says. “Now we only use about 80 percent of our resources, and the other 20 percent are doing jobs that we normally wouldn’t have gotten done.”
While he says he won’t see the differences in actual labor costs until next year, Johnson says he is expecting significant savings. That will contribute to the three-year return on investment (ROI) for the system, which cost a cool $1.3 million for all cost, material, labor and electrical.
“When you pencil it all out as just a straight line, the ROI doesn’t come out as quickly, but then if you look at the improved quality and the other aspects of the system, and what it’s given us the capabilities to do, that’s where the real payback is.”
The operation will be expanding its 16-acre perennials facility, with an additional six acres next spring for both annuals and perennials production. Johnson says he’ll consider adding another shipping system at that location, as well.
“It not only made us more efficient on the pulling side, it also made us more effective and efficient on the production side, so my team wasn’t as tired,” Johnson says. He adds, with a laugh, “I never thought I’d hear this in the spring time, but they were complaining because they weren’t getting enough overtime.”
Learn more about the Echo-Veyor system by visiting the Cherry Creek Systems website.