How Quality Greenhouses Lives Up to Its Name
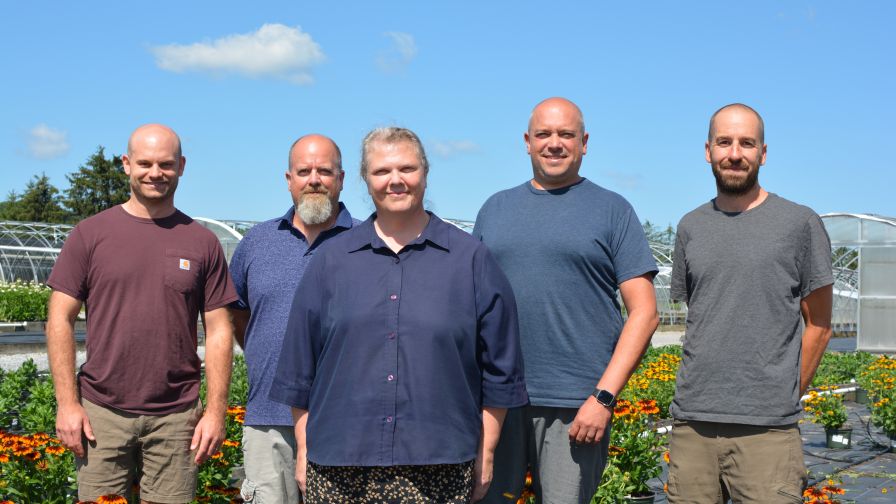
(From left): Jordan Reed, Lane Olt, Mary Myers, Brett Lebo, and Doug Nixon; Photo: Missy Zile
In any business, the tough times either make or break a team. Quality Greenhouses and Perennial Farm, winner of Greenhouse Grower’s 2023 Medal of Excellence for Operation of the Year, dealt with two tragedies, but those unfortunate events brought the team closer together. Now stronger than ever, the team at Quality is ready to tackle whatever challenges come their way.
In 2013, Co-founder Jeff Reed passed away during a triathlon. Co-founder Gary Lebo lost his battle with pancreatic cancer in 2019.
“After both of those losses, the team rallied together to grow the business and continue their legacies,” says Brett Lebo, President of Quality Greenhouses, and son of Gary Lebo.
Lane Olt, a longtime staff member who is the shipping manager, says the operation took a “punch to the gut” in losing both founders at an early age. However, after a time of grieving and absorbing the shock, the Quality Greenhouses team demonstrated fortitude and resiliency by not only resuming the work, but achieving new heights in sales and production.
“There was a lot of upheaval at that time, but everyone stuck it out,” says Jordan Reed, son of Co-founder Jeff Reed. “It’s really a testament to the type of people we attract — people who are willing to go through hard times and celebrate after we’ve made it through.”
Quality Greenhouses never lets life get in the way. The company has expanded almost every year since its inception in 1986, and there are plans to add 24,000 square feet of controlled-environment production space for the 2024 growing season. This will bring Quality’s grand total to 1.16 million square feet of controlled-environment production space, along with 25 acres of outdoor space across three locations in Pennsylvania: two in Dillsburg and one in York Springs.
Quality is known for its wide variety of offerings, including annuals, perennials, foliage plants, succulents, grasses, groundcovers, shrubs, poinsettias, herbs, and vegetables. As No. 57 on Greenhouse Grower’s 2023 Top 100 Growers list, this operation is known as a one-stop shop, where independent garden centers can fill their benches.
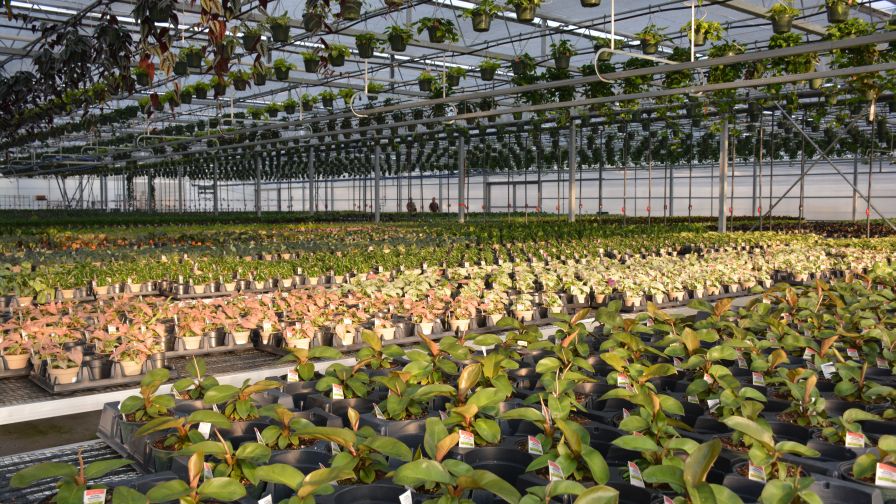
Quality Greenhouses and Perennial Farm has 1.16 million square feet of controlled-environment production space.; Photo: Missy Zile
Strides in Production Efficiencies
Not all production efficiencies are found in buying new technology, Lebo says. Although new technology does have its benefits, it can often be challenging to implement through several large facilities. Quality has made many gains in the last 15 years by streamlining its production processes in various ways.
Head Annuals Grower Chris Wallen says there were major labor savings in buying rooted cuttings for mums. Before Quality bought rooted cuttings, employees propagated their own mums. There was previously a lot of handling, including multiple shearings.
“We grow well over 100,000 2-gallon mums, and many other sizes. The labor savings was tremendous,” Wallen says. “We didn’t have any decline in quality or decline in the percent of sell-thru. It was a win for us all around.”
Zonal geraniums are another major crop for Quality. Employees used to root callus cuttings in the propagation house, then transfer them by truck to another growing range, requiring drivers and trucks. Instead, the team began direct sticking the geraniums in the greenhouse, eliminating the need for the propagation house and reducing the dependency on drivers and trucks.
“That was pretty big,” Wallen says of the change. “It saved a tremendous amount of man hours.”
On a similar note, Wallen says one of the growing ranges had no dock or potting equipment. All crops that were being grown in that range were transferred to a different range with a dock and potting equipment, which eliminated all handling and trucking for that plant material.
For the last 10 years, Wallen has segregated crops by growing requirements. Crops are separated based on their ideal growing media, fertilizer, and temperature, for example, which helps in maximizing the use of their space.
“When we open a growing space, we try to fill it as full as possible as quickly as we can and turn it as efficiently as we can,” Wallen says. “A lot of it is to try to reduce double and triple handling to reduce the amount of time that hands are on the crop.”
Inventory Software Gathers Data
In 2021, the need for new software to track live inventory and offer online ordering was clear. Quality had inventory management software, Reed says, but it did not track the inventory changes in real time. Quality posted its availability every Friday and customers submitted orders over the weekend for delivery the following week. By Monday, the inventory count was incorrect. After an especially busy season in 2020, the team decided to find new software. Reed was tasked with implementing new inventory software, which he says is a “huge shift,” in a good way.
Office Manager Mary Myers says the new software has made a world of difference. As the first line of defense when customers call with questions about their orders, she says a significant burden has been lifted from the office.
“It improved our ability to contact customers with questions and delivery information,” Myers says. “I’ve noticed a general change from being on the phone to a lot of emails and texts. That is easier for the customers.”
In addition to improving Quality’s customer service, Myers says the software provides valuable data to the team. For example, the sales team can look at how each crop is selling this year compared to last year. Wallen says Quality is still working through all of the available data, and growers use it to determine what crops to grow next year.
One of the best pieces of data, Wallen says, is the crop timing. This software records the number of days between the potting date and the availability date. It also records the number of days between the availability date and the sell-out date.
“We used to have heated discussions about how long a crop would take to finish,” Wallen says. “Now we can just look back at our data.”
The software gathers data on the number of flats sold on a particular day at any specific price point. If a customer wants a crop showing “buds and color” on a particular date, growers can use the data to work backwards and determine when the crop should be started.
For the 1% of the crop that is dumped and discounted, the team can see the efficacy of the discounts. Data showed that it is best to put plants on a smaller discount sooner, rather than wait until the demand has passed and offer a bigger discount.
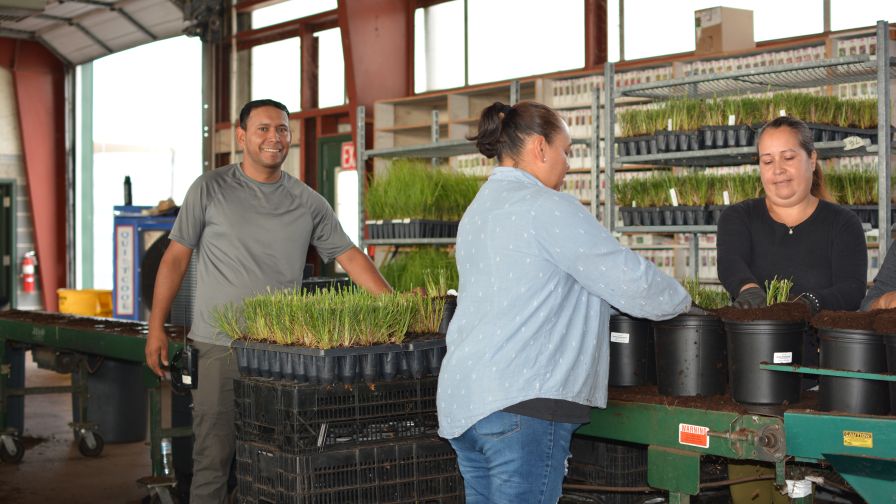
H-2A workers are a critical part of the team at Quality Greenhouses and Perennial Farm.; Photo Missy Zile
H-2A Workers Integral to Team
Quality Greenhouses has used the H-2A guest worker program for 20 years, Lebo says, adding that the guest workers are an essential part of the team. This year, Quality had a total of 235 employees, including 65 full time employees, 84 H-2A workers, and 86 domestic seasonal workers.
“This year, we had 84 H-2A guest workers, and almost all of them are returning workers,” he says. “They can come in day one and hit the ground running. They don’t need training. The H-2A guest worker program is absolutely critical to our success.”
Olt, who has worked at Quality for 37 years, says H-2A workers play a key role at the operation. He recalls one year when the guest workers didn’t arrive until the third week of May, when they typically come in March, and described that season as a tough spring.
For a number of years, the founders of Quality went to Mexico to visit some of their employees and meet their families. Quality employee Michael Thuma has grown into the key person overseeing the H-2A program, using his fluent Spanish to maintain the relationships with the workers while they are home in Mexico.
“It’s humbling to see that they’re willing to give up, in some cases, nine months of their year to work for us to provide for their family,” Reed says. “To grow the program, it’s all been word of mouth. People who have been coming the longest say they have a brother who wants to come, or multiple generations come. That’s partially because we treat them like our brothers.”
Olt recalled a story of an inspector coming to see the H-2A housing, and Gary Lebo was leading the tour. The inspector said that the H-2A housing was nicer than his own house, to which Gary responded, “They’re guest workers, so we treat them like guests.”
Reed says the work ethic at Quality Greenhouses and Perennial Farm focuses on flexibility. His father and Gary Lebo discouraged job titles, and suggested that all employees help each other.
Quality’s team members are the key to their success. By placing the right individuals in the right places, they can build the company internally. Staff members have the freedom to explore new topics that interest them, leading to professional development. Lebo encourages fellow growers to “trust your people”.
Interns on the Rise
Like every greenhouse operation, Quality has faced challenges with recruiting and retaining domestic workers, but Brett Lebo is proud of the company’s progress. Several young growers served as interns at Quality while in high school and came back to work full time. The operation has strong ties to the local high school, and one or two interns come every year. Quality is also developing an internship with local colleges, including Messiah University, York College of Pennsylvania, Penn State University, and Delaware Valley College.