How Plant Cuttings Automation Continues to Evolve
If you ask almost any leading greenhouse ornamentals producer about which technology has had the biggest impact on their success, chances are they will mention one of the cuttings sticking machines from the ISO Group or Visser.
Here’s a closer look at how growers are using the ISO Cutting Planter 2500 and the AutoStix to improve efficiency, and how each supplier is continuing to address evolving grower needs.
Imagery and AI in the ISO Cutting Planter
Since its introduction in 2016, the ISO Cutting Planter 2500 has had three major advancements, according to Raymond van den Berg, President of ISO Group. The first was the introduction of the ISO Cutting and TransPlanter system, which makes it possible to transplant cuttings with the same robot, making the machine even more versatile. The system works for pots and trays and has applications not just in the ornamentals market, but also in the herbs and soft fruit markets.
Another update is a gripper technique that employs four different types of grippers to accommodate the range of plant sizes, from small tissue culture cuttings to larger woody types of cuttings. The grippers are interchangeable, making the machine suitable for multiple seasons, van den Berg says.
The third advancement is the software. Van den Berg says the algorithms improve each year, resulting in a faster machine that is more versatile for multiple types of plants.
“We see that growers are adding more machines each year,” van den Berg says. “We also see that operators are getting more experienced with the machines, which helps them improve the speed and quality of sticking.”
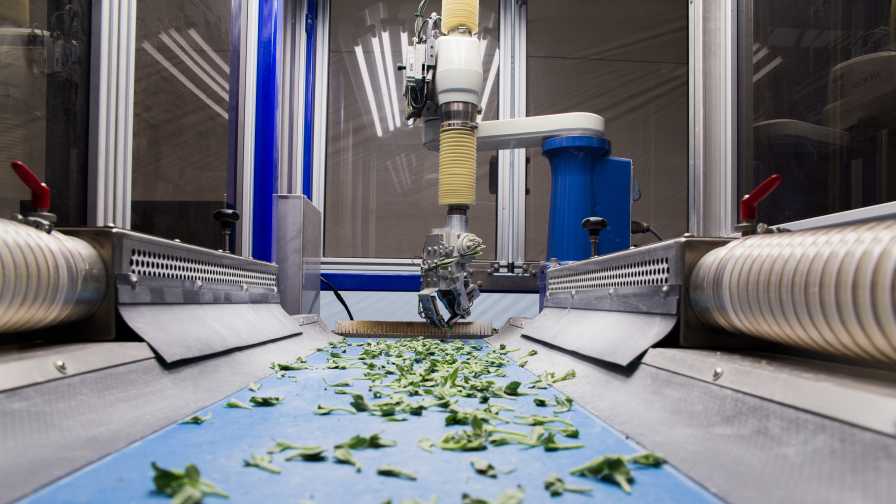
The ISO Cutting Planter 2500 employs four different type of grippers for all sorts of size plants, from small tissue culture cuttings to larger woody types of cuttings.
Photo courtesy of ISO Group
So, what can growers expect next? Van den Berg mentions three areas of customization, the first two are optional, and the last of is on the horizon.
Better rooting. “Growers who used the machine were looking to add rooting hormone to the cutting and automatic sanitizing of the gripper, so these features can now be added upon request.”
Smaller batches of plants. “With a grower’s specific setup, we help them cope with smaller orders and different types of trays.”
Adding cameras. “ISO Group is investing in artificial intelligence and plant handling techniques for optimal plant recognition. With the knowledge we get from building these machines, we are able to apply new insights into the ISO Cutting Planter machines, as well.”
More Grippers, More Media Options
Since its introduction, the AutoStix cutting program has proven to be a time and cost-effective means to fulfill strip transplanting needs, according to Sara Ross, Marketing Coordinator at Visser/Bellpark Horticulture. Not only does it reduce the number of workers required (a critical concern during a time of social distancing), it also ensures the end product will be consistent and of the highest quality.
Among the recent updates made to the AutoStix program is the Media Strip. This new strip has a glue plug in the bottom of each cell for the cuttings to be positioned in. Select growers have signed on for trials, and the initial test results are promising, Ross says.
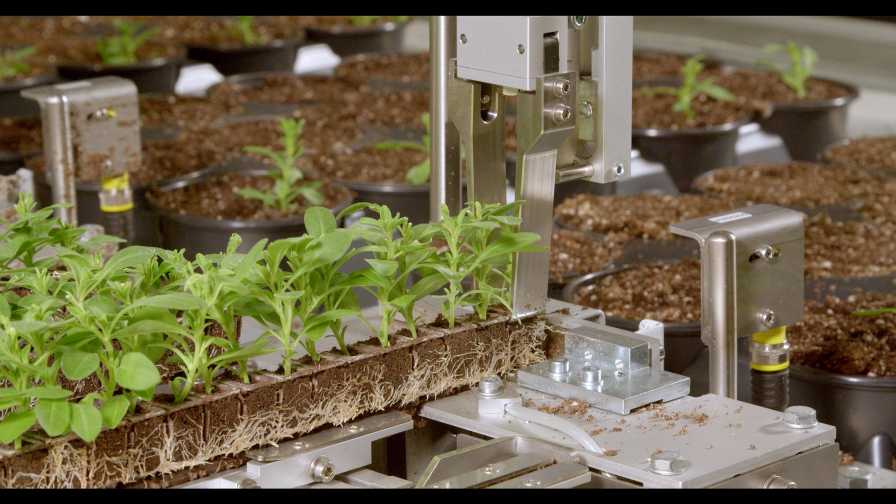
Since its introduction, the AutoStix cutting program has proven to be a time- and cost-effective means to fulfill strip transplanting needs.
Photo courtesy of Bellpark Horticulture
The AutoStix currently has two size options available: the traditional 6G machine with six grippers and 150 square-foot area, and the newer 3G machine with three grippers and a 107 square-foot area. The 3G is a great option for growers with more limited space, and it is a more economical solution than the 6G. Currently, Visser is also working on the development of the AutoStix XYZ that will be able to utilize omni-directional grippers to transplant multiple plants of various colors in pots while maintaining continuity.
“Visser is making continuous developments to the strips, with new varieties being added in the future,” Ross says. “With the ever-changing dynamic of the world, we must strive to improve our methods of growing and the AutoStix is the machine for the job.”
Growers Cite Production Gains
As suppliers of cutting automation technology continue to tinker with design and make improvements, the growers who use them are also looking for ways to become more efficient.
“The primary benefit to sticking with ISO machines is higher productivity than manual sticking, which is very important during this period of paying high H-2A wages and difficulties of finding willing local workers,” says Gail Berner, Manager of Propagation at Spring Meadow Nursery. “COVID-19 restrictions put even more strain on our ability to handle adequate weekly output, and we could never have achieved what we did this year without our four machines.”
Depending on the container, the ISO machines can output 35% to 50% more per person than manually sticking the cutting, and its productivity is much higher with larger runs of material.
Future improvements to consider, Berner says, would be a higher percentage of cuttings stuck (fewer misses and fewer cuttings getting passed over without being stuck) and faster sticking.
“Our woody cuttings present challenges that aren’t present with annual and perennial cuttings, so our speeds are on the lower end compared to sticking annuals and perennials,” Berner says.
To make sticking with machinery work, Berner says changes must be made to the cutting specs.
“We take all cuttings on site, so this required a lot of trialing and training to get uniform and smaller cuttings (where possible) than we used to take,” she says.
At Pleasant View Gardens in Loudon, NH, Production Manager Mike Goyette says he can run robots on multiple shifts 24 hours a day with a small team, and the cost per cutting stuck is lower on robots than manual due to hourly wages rising.
“The more you can work with the robots on setting them up to understand what each variety looks like, and the more you work with your unrooted cuttings suppliers to spec out what the robot cuttings should look like, the more successful you will be (i.e., remove leaves from the lower stem to about 10 mm and remove large leaves that may cover up the basal stem),” Goyette says.
Moving forward, Goyette says he’d like to see continued development of the software to improve cutting recognition through the cameras, which will help improve error rates on sticking.
“We would like to see multiple robots per cabinet to improve speed without doubling the cost of the entire robot cabinet,” Goyette says.
Award-Winning Innovation
The ISO Group’s latest innovation is also an award winner. During the 2020 GreenTech Live and Online event in October, the company’s ISO Grade 8000 won the Best Innovation award as part of the Innovation Awards presentation. The ISO Grade 8000 sorts young plants based on artificial intelligence and 3D imaging. This makes the sorting process more accurate because growers can sort on several different characteristics of the plant. With a unique gripper technique, it is also possible to pick up young plants and place them in an empty tray.