Seven Lessons Learned Over Seven Years in the CEA Industry
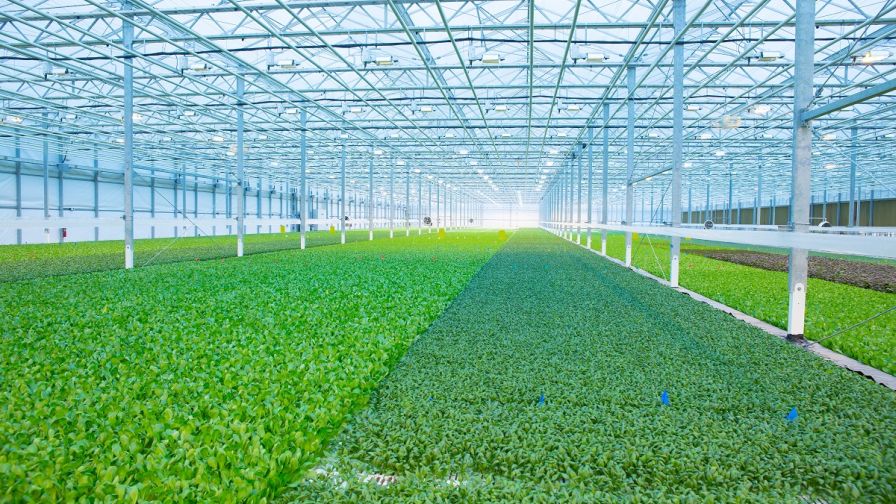
Photo: ARCO Murray
Note: This article was provided by Patrick Hidder of ARCO-Murray and the Resource Innovation Institute.
Controlled environment agriculture (CEA) facilities are complex operations that require careful planning and execution. If there’s one thing I know for sure after seven years in leadership at ARCO/Murray, it’s that to ensure the success of your facility, it’s important to consider various factors.
Here are seven key lessons I’ve learned from seven years of experience in CEA construction.
Assemble the Right Team
Choosing your team and partners before picking the site for your CEA facility can help mitigate risk and ensure you have the right resources to support your operation’s development. The core team of any facility design/build project starts with the facility’s owner, a contractor/builder, and an architect. These people should be able to guide the owner with hiring specific engineers relevant to executing the project. If you do not have a general contractor who does both design and build, you might also need to contract with an architect and civil engineer.
Finding the right partners for these projects starts with knowing they have experience in CEA. As Resource Innovation Institute shared in its Controlled Environment Agriculture Facility Design & Construction Best Practice Guide, “professionals selected for your CEA project team convey an understanding of the dynamics of CEA facilities. They empathize with the unique needs and solutions of growers and are able to translate their needs into construction terminology. Experienced CEA professionals can plan projects in a way to allow phased growth during operation without creating conflicts with operational activities or blocking future development.”
Consider crop specificity a luxury rather than a necessity; 90% of what you need is knowing the space versus knowing the crop. And if you want to be scalable, you have to pick somebody who is willing to go with you to other places — not someone who is just interested in the short-term gain of one project, but rather someone who is committed to your overall success.
Talk with Utilities Early
Engaging franchise utility partners early can help ensure access to power, water, and other resources, preventing delays in becoming operational. Energy consultants and/or utility engineers can be extremely helpful in catching early pitfalls such as capacity issues, or expansion limitations that could hinder a phased buildout, or identify capital investment requirements, like needing to build a substation to power the facility.
Utilities sometimes offer worthwhile incentives for system efficiency upgrades. To maximize your access to those funds, you have to begin the research early. For example, sometimes you can get double your incentives if you install your HVAC or lighting upgrades over two calendar years.
Measure Twice, Build Once
Setting aside enough time to plan and design your facility carefully, including defining the scope of your project and choosing vendors and suppliers, can help you avoid costly mistakes and ensure your facility meets your needs.
As outlined in RII’s Controlled Environment Agriculture Facility Design & Construction Best Practice Guide, costs to build a new greenhouse construction can vary from $50 to $150 per square foot for traditional designs, $150 to $250 for advanced vented systems, and $250 to $400 for advanced sealed greenhouses.
Owners will encounter bids from design and construction partners with widely different price tags and scopes. Forgetting to consider, for example, excavation needs in a greenhouse installation project and opting for a partner that doesn’t specifically mention that as a part of a scope of work can end up costing you more, as the excavation project now has to be quoted separately with new service providers.
You need to give yourself time when you bring that team together to sit down and say, “what are each of you responsible for?” That way, you can make sure that at the end of that meeting, your direct vendors, your general contractor, and any other relevant parties have all the costs and scope necessary to turn over a working building.
Design for Optimization
Designing your cultivation facilities from the inside out, considering everything from layout to equipment, can create a space optimized for efficient and effective cultivation. Consider needs such as coolers, conveyance systems, clean rooms, and racking before you finalize designs.
It may sound easy to simply move a wall or beam to accommodate a pack line in a leafy green greenhouse operation, but it can cost up to five times more to make the change after the fact than it would have cost to design the greenhouse with that system in mind in the first place, as greenhouses often are custom-engineered systems.
Consider Output
For fully integrated facilities with multiple manufacturing and processing activities, more engineers and consultants might need to be involved in the design and build process. Facilities with food product manufacturing capabilities will need to engage with food and safety engineers, while extraction labs will require hydrocarbon and/or ethanol process engineers to closely collaborate with your team’s civil and systems engineer.
Beyond that, there is a plethora of other considerations from cultivation type (are you growing in pots on the ground, or on benches? What are your drainage needs in each scenario?) to product types (are you producing a kosher product?).
Understanding your product and cultivation needs before sizing your building can ensure you create a facility with the right features to support your operation.
Leave Time for Review at Every Step
Reviewing your facility design early and often can help ensure a clear blueprint and prevent delays during construction.
Doing so can also help you keep tighter control on design and construction costs. If you make a change early in the design process, then stakeholders later in the process (safety engineers, tissue culture lab designers, HVAC suppliers, etc.) can build the change into their initial plans, rather than having multiple partners make changes after they had already committed to defined scopes of work.
Avoid Changes During Construction
Making facility additions or changes is one of the most expensive mistakes a CEA operation can make during the construction phase, as any change done during construction can cost orders of magnitude more than changes made during the planning and design phase.
Take for example, a simple trench drain placed near a pack line for cleaning purposes. Asking an engineer to move the drain on a plan costs $0. But if you are about to submit your plans for a permit and ask to move it 30 feet, your plan designer can charge you for the hours spent making those changes. If the change is decided before a concrete slab is put down, extending the drain another 40 feet can cost in the range of $100 per foot. But if change is made after slab is poured, moving that drain 30 to 40 feet might force you to jackhammer the slab and cut (and potentially destroy) pipes, costing you anywhere from $20,000 to $30,000, not counting any opportunity costs due to construction delays. All for a shift of no more than 15 yards.
Understanding the complexity and implications of changes during the construction process can help you avoid costly and time-consuming changes and stay on schedule.