The Future Of Automation: Q&A With Harvest Automation’s John Kawola
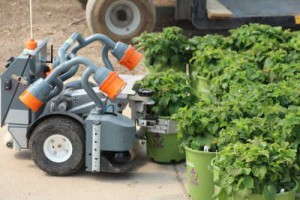
Harvest Automation’s pot-moving robots
Will the greenhouse of the future be full of robots with no human workers? What will be the next technology to reinvent greenhouse production? Learn about these and other predictions on the future of greenhouse automation from John Kawola, CEO of Harvest Automation.
GG: How did the folks from Harvest Automation get into this industry?
Kawola: The people who started Harvest Automation came from the robotics space and with a bigger picture vision that there’s a lot of difficult, heavy drudgery kind of work out there in the world. Here we are in the year 2013, and with all the technology in the world you wonder sometimes, “Is there a way to automate these things in some reasonable way?” especially when the work is not necessarily high-value work or requires a lot of decision making or dexterity.
That approach Harvest Automation took is a little bit contrary to how the general robotics industry has evolved in the last 10 to 15 years. There have been a lot of robotics companies founded that try to do the most difficult, technical work and they failed. It’s hard to do. The company was founded on the premise of finding the monotonous, heavy lifting in the world and seeing if we can automate that. When they surveyed several industries, they found that agriculture was very much front and center as a sector that still had a lot of manual labor.
Big crops like corn and wheat have already been mechanized. But there’s the whole other section of agriculture like fruits, vegetables, tree crops and the wine industry and the nursery and greenhouse sector that stand out as being high-value crops, however you measure it, by acre or per dollar input, with a lot of manual labor. That’s where they got started picking a sector to enter.
Then if you take the subsegment of that, the nursery and greenhouse sector as a whole is a lot bigger than any single crop. Moving containers around in the nursery and greenhouse for spacing, consolidation and collection is a huge task. You take all the workers in a nursery or greenhouse and that’s the last work they want to do. They would rather trim and prune or spray chemicals than move plants around. So that was really the premise of how Harvest Automation found the nursery and greenhouse niche.
GG: What new developments in robotics and automation may have applications in horticulture or agriculture that we should be watching out for?
Kawola: There have been significant advances in sensor technology. We think there are two things that need to be considered when thinking about sensors. One is what is it actually sensing and how well does it do that? Two, how is it deployed? Are these handheld sensors or permanent sensors?
We believe having permanent sensors in nurseries and greenhouses is not really practical. You’re creating a crop that’s in a container, that’s getting moved around and then shipped out the door. We see the adoption of using sensors in things like our robots as being an essential extension of what we’re doing today. Robots may be moving containers around, but they may also have sensor technology on them that could judge water content, pH, all the things that go into the health of the plant, right at the plant level.
If you can do it cheaply enough and fast enough, you can get down to gauging the health of every plant, instead of testing one out of every hundred or thousand. You might be able to get to the point where the incremental cost and time of growing every plant is basically zero, therefore the quality of the information and the plant can go up. If nurseries and greenhouses can move the price from $10 to $10.50, it’s a big deal. Any technology that can be deployed to help them do that should pay off.
GG: If growers have applications that they need automated, how do you suggest they work with companies or universities to develop new, innovative technology?
Kawola: I think what’s helpful is if the grower can communicate the magnitude or quality of the problem and quantify it in some way. To say, “We’re doing it this way now. We believe it’s inefficient and believe it could be more efficient with automation. We can imagine that if you apply automation, we could cut our cycle times in half. and that will save us one dollar or one cent per plant.” That really helps the discussion and helps to put the problems front and center with people who can help them solve that problem. So to the extent that growers can try to quantify the value of the problem, for a commercial entity like Harvest, we have to pick and choose the things we can work on — a quantified problem we think we can solve and would be of value to the grower.
Sometimes people think about robots doing a task. That’s what our first robot does, but now with information technology, we can add what we call an information layer. Our robots have WiFi. They can talk to the internet. The robots can be doing a task but also collect information at the same time. In the nursery and greenhouse space, we’re just starting to roll out the information layer for our first customers in a beta trial to see if they value it for inventory control. Robots are moving things, but they’re also counting. You’re capturing that information and you can upload and import it into your ERP system.
Those are the things that stretch our imagination a little bit. We think about creating a robot that does a specific task, we also try to think about what else it could be doing at exactly the same time with information technology.
GG: How do you think the greenhouse industry will be automated in 30 years? What other applications will be automated and how? Go nuts – what are your wild and outrageous predictions?
Kawola: A lot of the technology, whether it’s sensor technology, processing power, vision systems, even into hand manipulators and being able to pick things up — if they’re not there today, they’re all on a track where you can imagine that things could be fully automated. From planting to moving containers around to the application of chemicals and water to harvesting, packaging and shipping — you could imagine that being totally automated 20 to 30 years from now.
Businesses have to change to be able to adopt, and not just in agriculture. Look at what’s happened in the nursery and greenhouse space, even in the last five years. The recession really beat everybody up in a pretty good way. The emergence of the whole portion of the business that was mainly tied to construction and landscaping really got hurt.
At the same time, the sophistication of the retail channel for nursery and greenhouse going into the big box stores is like night and day compared to six or seven years ago. Those are both positive and negatives for greenhouse owners. The ones who have kept up, using not only automation, but other new techniques for merchandising and marketing, will come out the other side. Every year or two or three, things are pretty different than they were three years before.
GG: Can we automate everything in the greenhouse?
Kawola: Maybe. I think there are reasonable economic constraints. In our lifetime, there are things that I believe people will do better than robots. Not only better, but probably more economically. For example, people come to us and ask why we didn’t choose picking strawberries as our first task. Our answer to that was picking strawberries is really hard, even for people. You have to decide whether the strawberry is red or green. That’s a hard thing for a robot to do. So is the manipulation of the hand. You have to believe that at some point a robot will be able to do that as good or better and cheaper than a person, but that that is not true today. It may take 10 to 20 years for that type of task to catch up.
I can see certain types of tasks being much more difficult to automate. That’s where you would have people do the high-value tasks and have the robots do the heavy lifting. If you ever watch people picking strawberries in a field in California, they’re only picking strawberries 20 percent of the time. The other 80 percent is walking up 500-foot rows with boxes of strawberries on their shoulders. You can automate that. That’s not that hard to automate. That’s the concept of having people and robots working together and having people do the high-value stuff and having robots do the drudgery.
GG: What about the greenhouse makes it easier to automate?
Kawola: From a technology point of view, not to take anything away from the engineers here who have done a lot of great work over the last three years, but picking up a pot isn’t hard to automate. We knew we could create a robot that does that cost-effectively, in a smart way and not run out of money. We’re a venture-backed company. That was one aspect of why we chose nursery and greenhouse.
The second is that it is more like a factory than most farming applications, and moreso in greenhouse than nursery. You have multiple inventory turns a year. It’s more of a continuous process versus corn. You plant corn once and harvest once per year. Most big combines sit in the garage for 11 months of the year. In nursery and greenhouse, they may not be working 12 months of the year, but they’re working 10 months a year, producing ornamentals and roses, bushes and shrubs in the spring, then mums in the summer and poinsettias in the fall.
Third, the value. By almost every measure, the value of the crop per acre or per square foot is the highest in nursery and greenhouse compared to any other place in agriculture. People do and should care about optimizing inputs as much as possible. If you can improve efficiency there, you’re improving margins on something that’s valuable.