10 Lessons for Enhancing Safety in Your Horticulture Business
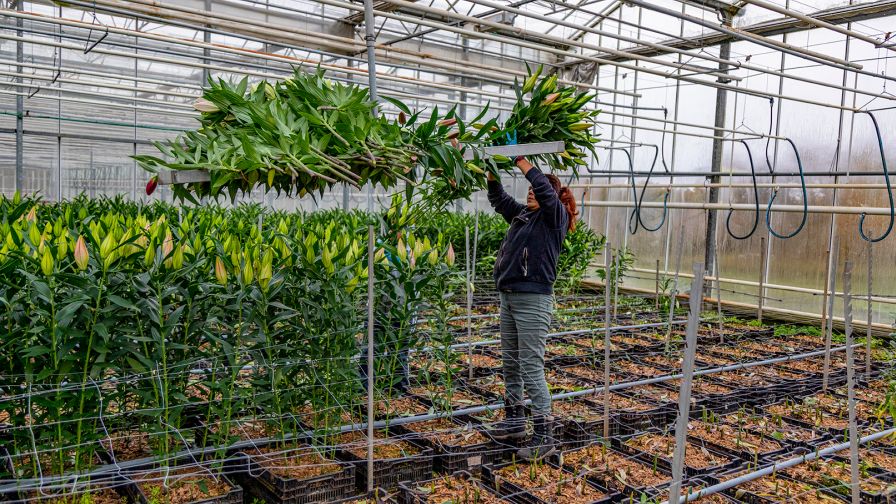
Photo: Hortica
Managing a horticultural business entails various challenges, including meeting customer demands and maintaining a thriving greenhouse. Amid these responsibilities, prioritizing the safety of your employees and customers is essential.
Soon, OSHA will release its report of the top 10 safety violations for the 2023 fiscal year. The annual report presents an opportunity to assess your own operations so you can make safety enhancements based on some of the most common safety risks faced by businesses like yours.
Let’s look at the 2022 OSHA report as a resource to cultivate a safer environment. It can serve as a valuable tool to enhance safety and mitigate risks within your horticultural business — one that nurtures the growth of your greenhouse alongside the safety of your employees and customers.
#1. Fall protection violations: 5,260 reported violations
For 12 consecutive years, fall protection violations have topped OSHA’s list of employer safety violations. Falls pose significant hazards in various industries, including horticulture. Ensuring proper fall protection measures, including guardrails, safety nets, and personal fall arrest systems, remains essential for safeguarding employees working at heights or elevated surfaces.
#2. Hazard communication: 2,424 reported violations
In horticultural businesses, employees may encounter various chemicals, fertilizers, and pesticides. Proper labeling, documentation of safety data sheets (SDS), and effective communication of potential hazards can mitigate risks associated with improper handling or exposure to hazardous substances.
#3. Respiratory protection: 2,185 reported violations
Respiratory protection violations underscore the importance of shielding employees from airborne contaminants such as dust, mold spores, or chemical fumes. Horticultural activities involving soil, potting mix, or spraying can generate respiratory hazards. Providing appropriate respiratory protection, including masks, and conducting proper training on their use, is essential to keep your employees safe.
#4. Ladders: 2,143 reported violations
Ladders are commonly used for various horticultural tasks like pruning, harvesting, and inspecting plants. Prioritizing ladder stability, proper positioning, and employee training on safe ladder use is essential to keep everyone safe. Ensuring the ladder is stable and secure before climbing, positioning it on even ground, and using proper techniques during ascent and descent are crucial steps to prevent falls and injuries.
#5. Scaffolding: 2,058 reported violations
Scaffolding violations highlight the risks associated with elevated work platforms. Although scaffolding may not be as prevalent in horticultural businesses as in construction sites, it’s still used for tasks like greenhouse maintenance and installation work.
#6. Lockout/Tagout: 1,977 reported violations
Lockout/Tagout violations emphasize the need to effectively control hazardous energy sources during equipment maintenance. Horticultural businesses may have various machinery and equipment requiring periodic maintenance. Implementing proper lockout/tagout procedures, employee training, and equipment-specific protocols can prevent accidental energization and protect employees from hazardous energy-related injuries like shock and chemical exposure.
#7. Powered industrial trucks: 1,749 reported violations
Powered Industrial Trucks violations pertain to safety issues with forklifts and other material handling equipment. These vehicles are commonly used for moving plants, pallets, or supplies in horticultural operations. Ensuring operator training, regular equipment inspections, and establishing safe operating procedures are essential to minimize the risk of incidents involving powered industrial trucks.
#8. Fall protection training requirements: 1,556 reported violations
Fall protection–training requirements violations highlight the importance of adequately training employees on fall protection measures and hazards specific to their work. Comprehensive training programs should cover topics such as recognizing fall hazards, proper use of personal protective equipment, and safe work practices when working at heights or elevated surfaces.
#9. Personal protective and lifesaving equipment–Eye and face protection: 1,401 reported violations
In horticultural operations, there are various risks that could damage the face and eyes, such as flying debris, chemical splashes, or exposure to harmful UV radiation. Ensure your employees have access to appropriate eye and face protection, including safety goggles, face shields, and protective glasses.
#10. Machine guarding (1910.212): 1,370 reported violations
Machine guarding violations serve as a reminder of the critical role it plays in protecting employees from machine-related hazards in horticultural operations. In a dynamic greenhouse environment, various machinery and equipment are used for tasks like trimming, cutting, or potting. Proper machine guarding aims to prevent contact between employees and hazardous machine parts that could cause severe injuries, such as entanglement, amputation, or crushing.
Recommendations for Enhancing Safety in Horticultural Businesses
The OSHA report underscores the need for proactive safety management and risk reduction across all businesses. Here are several ways to achieve this:
- Developing a comprehensive safety plan: Create protocols, procedures, and guidelines tailored to the specific hazards in your greenhouse environment.
- Conducting regular safety meetings: Schedule routine safety meetings with employees to discuss safety protocols, address concerns, and provide ongoing training on safe practices.
- Implementing safe hiring practices: Prioritize hiring individuals who demonstrate a commitment to safety and adhere to proper safety procedures. Conduct thorough background checks, including checking references and verifying qualifications.
- Integrating safety training into onboarding: Provide comprehensive training on hazard recognition, proper equipment usage, and emergency procedures as part of new employee onboarding.
- Fostering constant communication: Encourage open communication among employees regarding safety concerns and suggestions. Regularly update employees on safety practices, policies, and any changes in regulations.
- Modeling safe behaviors: Lead by example and consistently demonstrate safe behaviors in the workplace. Encourage employees to follow suit and create a culture where safety is a shared responsibility.
- Celebrating successes: Recognize and celebrate achievements in safety compliance and incident prevention. This positive reinforcement builds a culture of safety and encourages employees to prioritize safety in their daily work.
Cultivating a Culture of Safety
Creating a culture of safety through continuous training and reinforcement is vital. Regular communication channels allow employees to exchange safety concerns and best practices. By promoting a work environment where safe behaviors are modeled, and safety successes are celebrated, businesses can foster a strong commitment to fall protection training and cultivate a positive safety culture.
Improving safety not only protects employees and customers but also safeguards the business itself. By prioritizing safety measures and reducing the risk of accidents, horticultural businesses can potentially avoid costly penalties, legal issues, and potential damage to their reputation.
To get started on the path to a safer workplace, contact your insurer today. Opening a collaborative conversation is the first step to securing a bright future for your horticultural business. Let’s cultivate a culture of safety and protect what matters most — your employees, your customers, and your business.