Expert Advice on Overcoming Last-Mile Logistics Issues When Shipping Plants
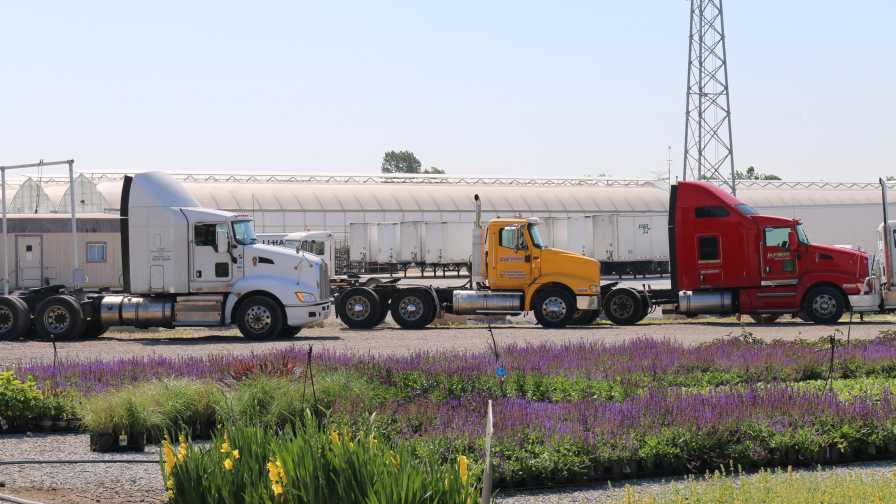
Since the COVID-19 pandemic disrupted the supply chain, growers have found creative ways to secure enough trucks for their shipments. Photos: Brian Sparks
Logistics are an ever-changing challenge for greenhouse growers. Many growers are expanding their presence in the e-commerce and direct-to-consumer markets for live goods, but there’s more to it than just delivering flowers. Packages must be delivered to the right customer, at the right place, at the right time.
Logistics includes a variety of factors, ranging from proper packaging to inventory management to ensure a timely delivery. The costliest leg of the trip, many growers say, is the last mile.
Dr. Stanley Lim, Assistant Professor in the Department of Supply Chain Management, Broad College of Business at Michigan State University, shares insights on challenges and solutions in last-mile logistics.
Challenges in Direct-to-Consumer Shipping
Lim says one major challenge in efficient last-mile logistics is the uncertainty and diversity of demand locations. As opposed to transporting truckload goods to fixed and few store locations, consumer orders are often in small quantities and in many locations.
“The physical distribution of goods in smaller quantities to a wide range of destinations not only presents logistical hurdles, which includes reducing the efficiency of routes, but also significantly increases transportation costs,” Lim says. “Both labor and fuel expenses contribute to the high costs associated with employing a vehicle and a driver to physically transport goods from one point to another.”
Lim underscores the growing challenges of last-mile logistics, particularly as the global population increasingly migrates to urban areas. According to a UN State of World Cities report, 70% of the world’s population will reside in urban centers by 2050. This demographic shift exacerbates the difficulties in last-mile logistics, as the concentration of demand points within similar locations adds to the existing complexity of delivering goods to uncertain and diverse destinations. Even though delivery locations may be in a concentrated area, there are many unique drop points.
“Various cities have begun to enforce diverse regulations, such as restricting vehicular movement, vehicle size, and even timeframes for transportation,” Lim says. “These regulatory constraints exacerbate inefficiencies and ultimately result in higher costs.”
By considering these factors in route planning, he emphasizes the importance of developing adaptable and innovative strategies to manage last-mile logistics challenges effectively. Lastly, consumers expect fast delivery, also known as the Amazon effect. Amazon set the standard for two-day shipping, and consumers are no longer appreciative of deliveries that take five days.
“When time constraints are present, logistics companies lose the flexibility to consolidate goods, which would otherwise reduce delivery costs to a single location. In the past, demand could be pooled across multiple days, allowing for a larger volume of goods to be delivered to a common destination, thereby reducing the cost per drop,” Lim says. “However, when faced with a narrow window of, for example, 24 hours, the ability to aggregate demand across multiple days is lost. Consequently, the number of deliveries to a shared location decreases, leading to increased costs
per delivery.”
Solutions for Efficient Logistics
Lim says a tracking and monitoring system, commonly referred to as a track-and-trace system, would benefit both growers and consumers.
“By providing real-time tracking and status updates to various supply chain stakeholders, including customers, potential issues can be identified early on, allowing for prompt interventions during transit rather than waiting for complications to escalate further,” Lim says. “This heightened level of visibility enables customers to anticipate the arrival of their goods more accurately, which in turn can contribute to an increased success rate for deliveries.”
Sometimes growers know when a delivery failed because the consumer rejected it, often due to damaged goods or the items were not fulfilled in proper quantities. When shipping live goods, packaging is key to protecting the plants.
“Growers can benefit from using specially designed containers that ensure adequate ventilation, reducing moisture buildup and maintaining optimal temperature and humidity conditions,” he says.
Moreover, Lim suggests that route optimization software may aid growers in streamlining the logistics of plant shipments. Software that incorporates GPS traces, traffic information, and driver local knowledge can help minimize travel distance and reduce fuel and transportation costs.
Harnessing the availability of big data, according to Lim, enables growers to build more accurate demand forecasting models for their operation.
“Accurate predictions of demand allow for the cultivation of an adequate supply, which in turn minimizes stockouts and fosters customer satisfaction,” he says.
However, he acknowledges that perfect alignment between supply and demand is rare, emphasizing the importance of investing in demand forecasting models to better plan inventory and minimize costly stockouts.
In the live goods industry, Lim recommends implementing a first-in, first-out (FIFO) strategy to ensure that each customer fairly receives fresh plants, reducing potential waste.
Addressing the challenges of logistics, whether shipping plants directly to consumers or retail partners, by tracking shipments, using route optimization software, and properly packaging plants, growers can reduce supply chain disruptions and enhance overall efficiency.