Why Small-Scale Growers Have a Great Opportunity in Today’s CEA Market
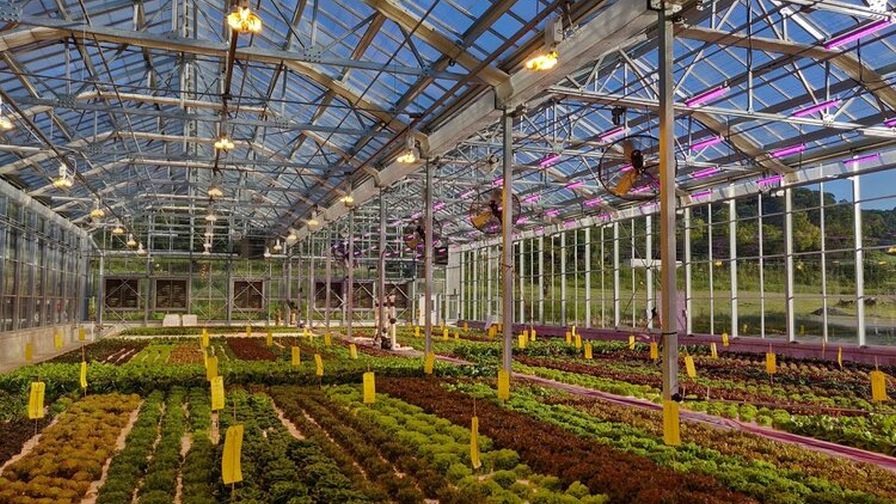
Photo: Greener Roots
On April 20, the GLASE program hosted an online panel discussion on controlled-environment agriculture from a smaller scale. These commercial greenhouses and indoor farms present a unique opportunity in a growing market. Attendees had a chance to hear successful small-scale growers discuss the challenges and opportunities of owning and operating a CEA facility.
Moderated by Brian Harris of Hort Americas, the panelists included Jeffrey Orkin of Greener Roots in Nashville, TN; Tyler Baras of Area 2 Farms in Arlington, VA; and Bob Jones of The Chef’s Garden in Huron, OH.
Below are just a few key insights from the webinar; you can watch the full recording here.
About Each Operation
The Chef’s Garden primarily markets to restaurants with a wide range of crops, and expanded to home delivery during the COVID-19 pandemic. It has about 125 acres of outdoor production and 15 acres of covered production. “We made the decision to wait on vertical farming, and thankfully have not gone down that road yet,” Jones says. “We’ve experimented with different lighting options, and settled in on dynamic LEDs that we can program.”
Area 2 Farms does home deliveries from its vertical farm in Arlington, and has been doing so for about a year. Baras previously worked with large-scale vertical farming and greenhouse operations before setting out to do his own thing.
Greener Roots started as an indoor vertical farm, then expanded to add a 10,000 square-foot greenhouse. It mostly grows leafy greens and herbs and is 100% wholesale. Most of the product is sold in Nashville, but the company sends a truck to Atlanta weekly. It has LED lights in both facilities, and HPS lights in the greenhouses.
The Role of Lighting and Other Technology
Orkin says Greener Roots has sensors to measure light levels in correspondence to outdoor light levels. A computer will turn the lights on when needed. The greenhouse has a mix of HPS and LED. “We get more blue spectrum from the LEDs, and this can make some varieties more prone to tip burn,” he says. “We do change the bulbs less with LEDs. We know there are some varieties we can’t grow well under LEDs, but some do very well.”
Jones says he is skeptical of lighting research that compares HPS to LEDs because “it’s apples to oranges.” He recommends growers try things at their own farm, with the understanding that every variety will be different in how it responds. “Green and red lettuces like different lights, and the timing of the crop also matters,” Jones says. “Dynamic control is a lot more efficient for us because we don’t rely on someone to turn the lights on and off or dim them. We only want to stress the crop at the end to pull out attributes like flavor and color.”
Area 2 Farms uses sole source lighting, and Baras says varietal response is important. “We grow a lot of different crops through our CSA program, and so we went with a broad spectrum to keep things gentle and avoid too many ranges of crop sensitivity,” Baras says.
Advice on How Small-Scale Growers Can Position Themselves for Competitive Advantage
Jones: “Know your market, and then plant to that market. Scale appropriately and understand what you can do effectively and still be profitable. Develop systems that work in your market and then scale.”
Orkin: “Know what your customers are accustomed to paying for your crop. I can increase prices if I have better quality, but I could not have entered the market with a higher price. People that don’t stay in business scaled too big too early. We’ve only filled what we can afford to pay for, which has forced us to build smaller systems and learn from them. Every system I have has been tweaked in some way, so thankfully they were small at the beginning.”
Baras: “Small-scale vertical farms seem to be the ones succeeding right now. You can keep your employees passionate and connected. Also, once you grow to a certain scale, the only option you have is wholesale, where you can lose control over prices. At a smaller scale, you can control more of that, and you can have a better connection with your customers.”
What Challenges or Opportunities Do You Face That a Large Grower May Not Face?
Jones: “Keeping your operation small enough keeps you out of labor shortage problems. Sometimes being small can be an advantage – it makes you more nimble. Many big operations have gone out of business because they didn’t have plant people on their team. We need to think like people who farm, but we also need to be business people who farm. Don’t just farm what is easy to grow. Know what your customers want, and meet or exceed their expectations.”
Orkin: “It can be challenging to align your staff to your cash flow. If you can nail your systems, you don’t have to have a highly paid, experienced grower to succeed. We’ve focused on variables like vapor pressure deficit and airflow, and then we focus on yield per square foot. We built a software to tie into our sensors and collect data that I can look at later and see which conditions resulted in the best crop. If you’re not a plant person, you can leverage technology to help you and your team, so you don’t have to pay a lot for an agronomist. With today’s labor market of constant turnover and staff changes, this is more important than ever.”
Baras: “Ease of operation is huge for a small-scale grower. In larger companies, you feel like you have to hire more experience. Being smaller can bring simplicity to whoever you hire.”
Technology That May Be Lacking in This Industry
Orkin: “We need sensors that are more cost effective. We have sensors, but they’re too expensive to have all over the farm. Weed someone to make simple sensors for air or leaf temperature, air flow, or light levels. In a greenhouse you can have sensors that cover a large area, but in a vertical farm the size of layers differ, so we need more sensors within. We can capture more data with them, but they’re expensive.”
Baras: “I would like dissolved oxygen systems that are simpler. If something is too expensive, we often end up building it ourselves.”
Jones: “The best sensor meter you have is the plant. It will tell you what’s going wrong. Knowing the conditions in your greenhouse is good additional information, but you can also get a sense for some things.”