5 Tips for Efficient Greenhouse Heating
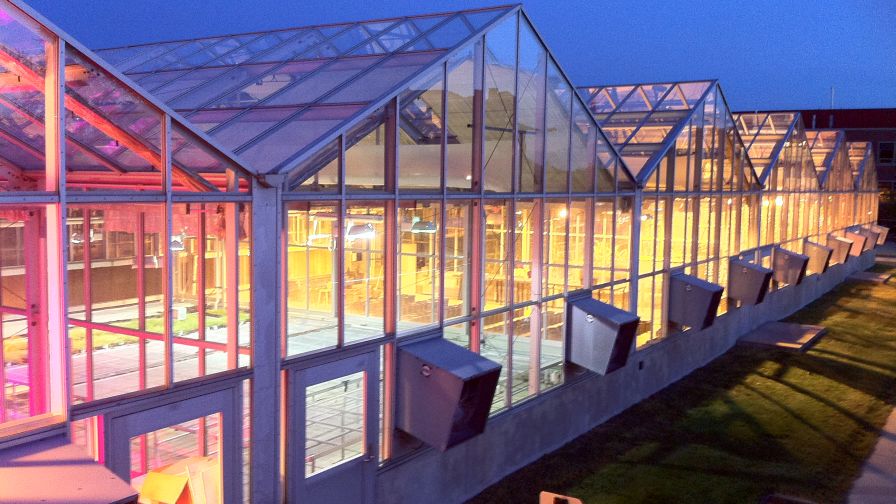
Photo: Rob Eddy
During the summer and shoulder months, cooling and humidity control can make up a significant amount of a greenhouse facility’s energy use. Traditionally, greenhouse operators would heat their greenhouses and open side and roof vents to exhaust humidity from the leaf surface. However, as energy costs have soared in recent years, these traditional (and oftentimes inefficient) methods are becoming increasingly expensive.
By doing this, “you’re throwing away a lot of heat,” explains Pieter Kruijt, Horti-division Director at Resource Innovation Institute (RII) member Verkade Climate. “While gas prices were low, nobody really cared. Nowadays, the gas prices, at least here in Europe, are about 10 times as high as they were two years ago.”
As such, operators increasingly are turning away from mechanical heating and cooling, opting instead for more passive and resource-efficient methods such as optimized airflow, desiccant systems, and building circular systems in-house or with partner industries.
Here, RII presents tips and solutions to help you optimize your greenhouse heating and ensure you’re running an efficient and profitable business.
Consider Heat Pumps and Cogeneration
Heat pumps can be a great replacement technology for gas boilers or propane heaters, especially for operations that have both heating and cooling needs. Heat pumps function by circulating a refrigerant – a hydrofluorocarbon HFC), ammonia, CO2, or the new generation
HFO (HydrofluoroOlefins), for example – using a compressor to influence its heat retention ability. The fluid circulates through the system, bringing heat to areas where it is needed and exchanging it for cold needed elsewhere (or vice versa).
They also generally are very efficient at converting electrical energy into thermal energy. Kruijt has seen systems capable of generating up to nine kilowatts of thermal energy for every kilowatt of electrical energy inputted (combining the value of both heating and cooling).
“For instance, phalaenopsis – the moth orchid – in certain regions, you need to cool the plants to make them spike,” Kruijt says. “So you need cooling capacity to let the plants do what they need to do. But it’s a year-round crop, so there’s always a part of the crop that is young plants. The other part is what’s being hardened and finished. If you can balance that heat load, then you can produce the cold for the cooling of the hardening part where they spike, and you can put the leftover heat in the young plants.”
Likewise, he adds, a produce grower might use the cooling capacity to store tomatoes or other perishable produce. The heat from assimilation lights can be used in other zones or even in a nearby greenhouse in a hybrid setup.
Combined heat and power (CHP) systems, also known as cogeneration systems, are another valuable technology to consider. These units generate electricity and heat that can be used on-site, and some utilities will purchase any excess energy they generate, offering a quicker ROI. While their use potentially runs counter to sustainability goals, CO2 can be collected from fossil fuel CHPs to minimize the carbon footprint impact.
“Cogeneration lends itself to being extremely compatible with greenhouses,” says Andrew Horowitz, Director of Strategic Development at RII member Kubo Greenhouse. “There’s a little more technology that goes into ensuring the quality of the CO2 is suitable for crops. Even though it’s an antiquated technology in some sense, that ability to use all waste streams efficiently turns it into actually one of the most efficient solutions because you’re able to utilize the combustion by-products at the source and then feed that power back to the grid.”
This added CO2 can be better retained during cooling periods in semi-closed/positive-pressure greenhouse environments compared to Venlo-style structures.
“The ability to dose CO2 while cooling is a significant advantage in resource efficiency,” Horowitz says.
Though a typical Venlo cannot enrich CO2 beyond the ambient level when cooling, it has the advantage of using passive ventilation, which eliminates the energy requirement for exhaust fans and pumps using evaporative cooling systems.
Look at Alternative Humidity and Temperature Control Systems
Higher humidity air requires more thermal energy for it to achieve the desired temperature. By lowering humidity ranges, operators can more easily heat and cool their plant growth environments. Mechanical cooling using traditional HVAC units is not common in greenhouse operations, but with the present gas cost, can be an efficient alternative to burning gas and venting humidity (and precious CO2) out of the roof. In Europe, at present gas prices, these systems can have a simple payback of less than three years, Kruijt says.
Instead of mechanical or other energy-intensive cooling systems, greenhouse operators can also consider desiccant systems using materials like silica gel. In these dehumidification units, humid air is drawn into the system via fans, where it comes into contact with the silica gel. Water vapor sticks to the silica’s surface in a process called adsorption. The filtered air is significantly drier, allowing the greenhouse operator to regulate the environment’s temperature more efficiently.
These systems are not without their own energy use, however: once saturated, the silica gel must be heated to release the trapped water outside of the greenhouse and for it to regain its adsorption capabilities. That said, combining these systems with a heat pump or other alternative heating method can generate additional efficiencies.
Buffer tanks are another effective tool that can help greenhouse growers better manage their environmental control system’s energy use. A buffer tank, also known as a thermal storage tank, is a container that stores hot water or chilled water (or another fluid) for later use. For example, hot water generated during peak boiler demand can be stored and gradually delivered to the greenhouse to prevent the heating system from frequently cycling on and off. The opposite can be done with chilled water.
“By running your chillers at times of the day where there is less stress on the grid and building up a buffer of chilled water, you can significantly reduce your facility’s monthly peak demand while increasing your resilience to extreme climate events. This can also translate to significant savings on your monthly electric bill, which is often based on both total electrical consumption and monthly peak demand,” Horowitz says.
Build Circular Systems When Possible
Designing a facility where waste or by-products from one process is used in another is referred to as a circular system. Greenhouse operations offer plenty of opportunities to build circular systems that maximize resource use.
For example, hot water drawn from a geothermal well could theoretically be used to heat the silica gel in a desiccant system, avoiding the need for a gas boiler or other energy-intensive heating mechanism to regenerate the gel.
Geothermal wells use hot water located up to 2 miles beneath the Earth’s surface.
“The water coming out can be 200°F, and all one needs is to harvest the energy by pumping that hot water to the surface,” Kruijt explains. “The operating costs are relatively low, but the initial investments to drill two holes – one to take the water out and one to put the water back in – can be more than $2 million per kilometer [$3.2 million per mile].” Large capital expenditures like that might make any consideration of such a project moot for 2-acre mom-and-pop operations.
Instead of generating their own additional heat or power, Kruijt advises greenhouse operators to look toward neighboring industries to see if there are opportunities to use some of their waste by-products in their own operations in a partnership that benefits all parties. Both heat and CO2 can act as feedstock for the plants, reducing carbon footprint for the neighboring industry, and helping the plants to grow.
There is “a lot of potential with excess heat from industry,” Kruijt says. “Let’s say a concrete production company bakes the limestone into clinker. There’s a lot of heat put into the process, and there’s a lot of excess heat being generated by the concrete plant,” in addition to high levels of CO2, he notes. “So there would be a big potential for greenhouses to consume that excess heat and excess CO2 from that industry, together you are becoming sort of carbon neutral.”
Allow the Plants to Do Their Thing
As industry and academic researchers continue to push the boundaries of plant knowledge, many are concluding that most crops can grow optimally within a wider band of temperature and humidity settings than previously thought.
“There’s been a new trend for a little longer than the past year where growers find that a crop can actually handle quite more than we think it can,” Kruijt shares. “So we also sometimes can just let the plants do what they do: They can take a higher humidity level, they can take more heat, but they can also take more cold.”
He says he’s starting to see operators allow greenhouse temperatures to drop to the mid-50s Fahrenheit overnight in the winter instead of maintaining temperatures within a band of 60 to 65°°, “but then accumulating more solar heat that we get for free during the day, so the average temperature of the crop is still the same.” (See Table 3 on p. 18 of RII’s HVAC Best Practices Guide for temperature and humidity ranges for a variety of crops.)
The same logic applies to humidity.
“As long as the plants are able to let that humidity go off of their leaves without stressing the plants too much, it’s all okay,” Kruijt says.
Additionally, these temperature and humidity requirements can vary as crops age. For example, “as leafy greens progress from their early stages to the teenage stage, the surface area of the plant increases and the transpiration can induce a cooling effect on that area of the greenhouse,” Horowitz details. “Understanding how the plants react and respond as a function of time and the growth cycle is important to ensure as stable of a climate zone for your crops as possible.”
Talk With Your System Providers
By talking with your system manufacturers and utility providers, you can lean on their experience and expertise to help cater solutions to your specific crop and local climate, as well as avoid costly mistakes that can spell ruin for your business.
Getting your vendors, design team, and utilities communicating early can help identify construction and feasibility issues early and allow you to course correct before investments can be recouped. Those early conversations will allow you to “determine the amount of energy that would be required as max capacity for the winter season, as well as an annual consumption based on a yearly average day temperature. Based on that, you can determine whether you can build 1, 2, 3, or 100 acres of greenhouse,” Kruijt says.
Horowitz says the main mistake he sees operators make is not designing a greenhouse that meets changing world conditions. He advises businesses to be “intentional about the potential need for future expansion. Even if cost is an initial restraint at startup, work to create the options that will allow you to create capacity in the future. For example, it’s always safer to overdesign when it comes to some of the larger underground cooling infrastructure,” he says.
For additional tips, insights, and best practices for optimizing heating and climate control in greenhouses, explore RII’s HVAC and Facility Design & Construction Best Practices Guides.