Supply Chain Disruptions Cause Shortages, Delays in Plastics Market
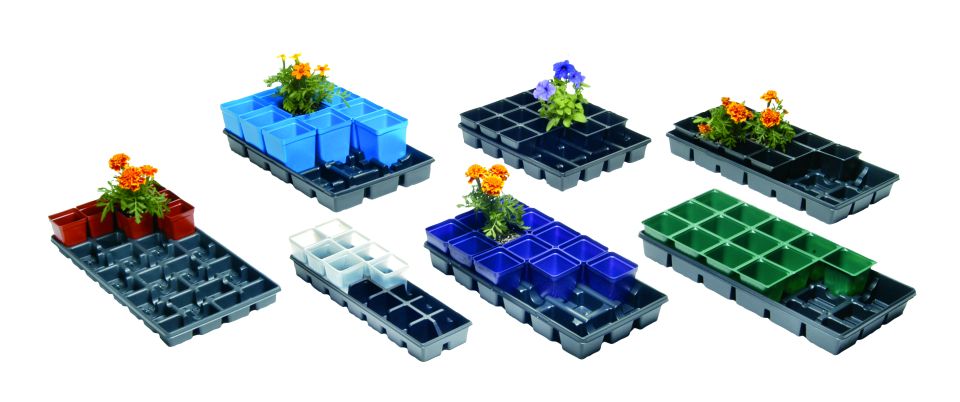
Landmark Plastic offers thermoformed trays and pots. Photos: Landmark Plastic
Every grower knows the importance of pots and propagation trays. Many of those materials are plastic, leading to a high demand for plastic and its raw materials. The last two years have been especially challenging due to the pandemic and the Great Texas Freeze. Limited supply coupled with shipping delays left many growers without enough pots.
Supply Chain Disruptions
Steve Beall, Vice President of Sales and Marketing for Landmark Plastic, says inflation impacted every aspect of the industry. The cost of raw materials, transportation, and labor have significantly increased.
A major factor that led to the current plastics market is the Great Texas Freeze in early 2021. About 80% of resin used for plastics is sourced from Texas and the Gulf of Mexico, Beall says.
“When the resin plants got decimated, then everyone’s supply chain was in peril,” he says. “The challenge to everybody was that prices doubled overnight.”
The two main raw materials are polypropylene, which is mainly used for pots, and polystyrene, which is primarily used for propagation trays. In the past, Landmark Plastic primarily purchased recycled plastic, known as post commercial waste plastic, because it is less expensive, good for the environment, and thus good for the industry. However, companies with scrap plastic found ways to reuse it themselves when input costs increased, which created new challenges sourcing recycled plastics. Beall says this led Landmark Plastic to source raw materials and use recycled plastic.
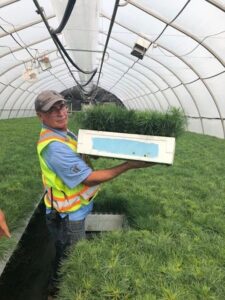
One customer from Beaver Plastics shows off his propagation trays, which Paul O’Neill says will last 10 to 20 years. Photo: Beaver Plastics
“It’s been a supply chain challenge because between the pandemic and what happened in Texas, the market has been slow to recover,” he says. “It’s the perfect storm. All the inputs have gone up and the person who ultimately has to pay the price is the consumer as the cost historically gets passed down.”
Landmark Plastic works to prepare for supply chain disruptions, Beall says, by keeping safety stocks of plastic in silos at its facility in Akron, OH. Hurricanes in the Gulf of Mexico have also caused delays for materials in the past.
Beall says the cost of labor has skyrocketed, and it is difficult to find enough employees.
Paul O’Neill, Manager of Grower Products at Beaver Plastics, says the company’s raw materials are sourced both locally and internationally. Beaver Plastics is headquartered in Edmonton, AB, Canada, and its suppliers are located in North America.
“As demand for lightweight molded products for construction and industrial uses increased, it has put a strain on existing manufacturing capacities. There is more demand and limited supply,” O’Neill says. “Products have become more valuable. Raw materials and shipping are available at a higher price.”
There are limited numbers of trucks, drivers, and trains, O’Neill says. But there is always a truck available to those who are willing to pay the price.
“You have to pay more for shipping,” O’Neill says. “If you’re waiting for rates that you got a year ago, you won’t get any.”
O’Neill says it is best to keep customers informed when there are delays. Input costs also continue to rise, including energy, raw materials, and shipping. He says pricing has increased at least 30%, depending on the product. It is necessary to plan in advance, and communication is key.