Greenhouse Dehumidification With Latent Heat Recovery Looks Promising
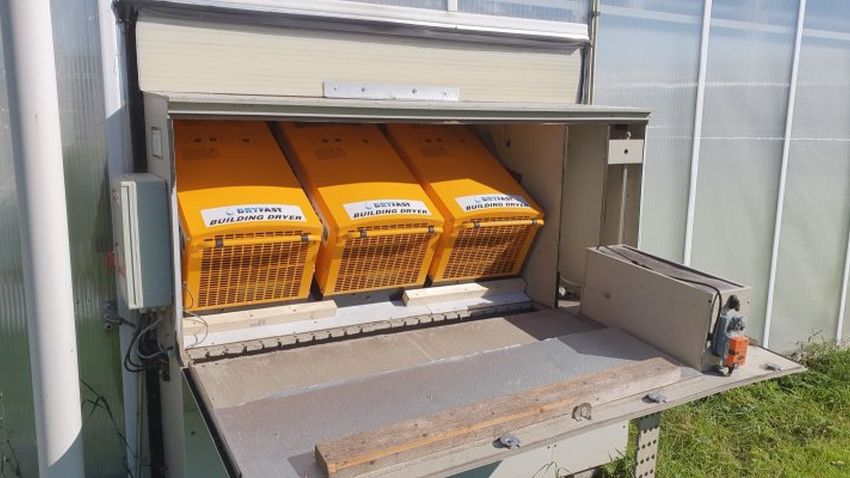
Photo: Wageningen University
High humidity in the greenhouse reduces crop transpiration and nutrient uptake and increases the risk of fungal diseases. This is why growers often keep the vents of the greenhouse open at least a crack most of the time. This carries off the excess humidity, but you also valuable heat and CO2.
To address this problem, the Greenhouse Horticulture and Flower Bulbs Business Unit of Wageningen University & Research (WUR) is investigating various dehumidification systems that can keep the greenhouse better closed. Results in a cucumber crop with such a system show a more than 60% reduction of heat consumption.
There are several ways to dehumidify the air in a greenhouse. Opening the vents a little, or inserting outside air with ventilators, are the most common. But with these methods, dehumidification compromises the design objective of a greenhouse, which is to create a closed growing space. By using outside air for dehumidification, the greenhouse is deliberately made leaky.
In recent years, several systems for internal dehumidification have appeared on the market. With such machines, heat and CO2 remain inside the greenhouse, and excess air humidity is converted to liquid water ready to be reused for irrigation. This system is principally equal to the energy saving heat pump-based tumble dryers. However, the existing systems are mainly intended for plants growing in pots and cut flowers. Affordable internal dehumidification systems for high-wire crops (tomatoes, cucumbers, peppers) are still unexplored territory.
That is why WUR is investigating the practical implication of a simple heat pump-based air treatment unit, tailored for high-wire cropping systems. The researchers refurbished an existing air treatment unit, originally intended for outside air intake, with three simple construction dryers. Together these provided a dehumidification capacity of 12 liters per hour, which is 24 grams/(m² hour) for the 500 m² test greenhouse. This allowed the greenhouse to be sufficiently dehumidified during cold periods and at night when the windows and screens were closed. With such a system, the greenhouse uses no more than 9 m³ of natural gas per m² per year, while maintaining normal cucumber production. That is less than 35% compared to the current standard. Of course, the system does use electricity, about 30 kWh/(m² year).
This autumn, WUR will work with Van Dijk Heating on a further improvement of the system in order to have the electricity consumption and/or gas consumption of the greenhouse reduced even further.