In Greenhouse Technology, One Size Does Not Fit All
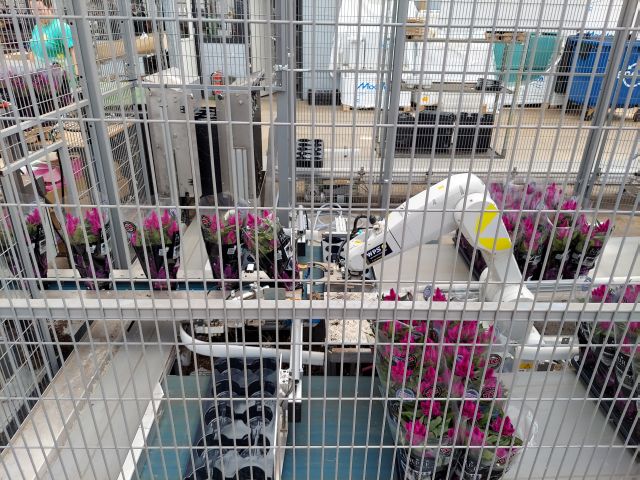
Ammerlaan-Sosef has reconfigured its internal logistics, keeping labor savings and bettering working conditions for employees in mind. Photo: Janeen Wright
I’ve never been a fan of the one-size-fits-all mentality where we place things into groups and expect that everything in that group is the same. Just like the hem of a one-size-fits-all nightgown puddles around the feet of a four-year-old girl while showing off the belly of her 32-year-old mother, one-size-fits-all seldom, if hardly ever, fits all.
The same is true for greenhouse operations. The solutions, the equipment, the greenhouse technology — there are plenty of possibilities out there. Yet, operations seem to have the most success when they take from that array what will work for the unique needs of their operation and customize those solutions or innovations.
In June, I had the opportunity to visit several Dutch greenhouse growers in conjunction with a trip to the Netherlands to attend the GreenTech tradeshow. Thank you to Ton Koers of Schoneveld for setting up these visits. We toured various-sized operations using different levels of greenhouse technology, mechanization, and automation. In every case, the goals and needs of the operations drove the investments in these areas.
The Schoneveld breeding and production facility in Wilp, the Netherlands, included electric cars and bikes, a closed water system with 100% reuse of raw materials, a microdosing unit, LED lighting, and a vertical fan (Hinovator) in combination with a ventilation jet system to provide outside fresh air replacement from the greenhouse ridge to the cultivation rooms. Schoneveld also cooperates with its neighbor for biogas and hopes to eventually combine natural gas with hydrogen gas for heating. This greenhouse was built for the future. Much of what it is equipped with reflects the company’s commitment to sustainability, something it has incorporated into the DNA of its business profile.
Ammerlaan-Sosef, a celosia, cyclamen, and primula grower based in Honselersdijk, has automated growing processes as part of its main strategy. In the summer of 2021, the operation added close to 3 acres to its nearly 7-acre cultivation space. It took the opportunity during this time to reconfigure its internal logistics, keeping labor savings and bettering working conditions for employees in mind. The result is nearly 100% logistics automation with conveyors all around, ISO machines, a pot spacing machine, a packing robot, automated grading, a sleeving machine, and more. While going through the process, management asked themselves some interesting questions: What jobs cause employees the most stress and discomfort? What jobs do employees call out sick on the most? Then it set out to change or eliminate those jobs with some of the equipment and automation it chose for the facility.
Annuals grower Gebr. Grootscholten, on the outskirts of Kwintsheul, is regarded as one of the highest quality growers in the Netherlands due to its high standards. It specializes in producing smaller numbers of plants intended for same-day trade. I would categorize it as more mechanized than automated. Aluminum tables run at waist height throughout the complex, to bring the plants to employees. Cuttings are propagated by machine, and by hand. Water is collected under the tables, screens have been updated, and diffuse glass installed and an auto-shading system have been installed. Geothermal energy also provides Gebr. Grootscholten with a sustainable energy source. All of this reflects the operation’s different needs as a grower of several different types of annuals in smaller lots.
Three different growers with varying goals and needs, all with one thing in common. They wanted personalized, customized greenhouse technology and automation solutions. When it comes to strategies, techniques, equipment, and technology investments, you are the only one that knows what is best for your operation. Don’t settle for one-size-fits-all solutions. Insist they fit your needs. Work with your supplier to make changes if needed or find a base to start with and keep tweaking it until you make the solution your own. You might even have to get innovative and create something new. Whatever you do, don’t be seduced by one-size-fits-all solutions as a replacement for what you really need — solutions that fit your circumstances.