Six Greenhouse HVAC Trends to Watch in 2023
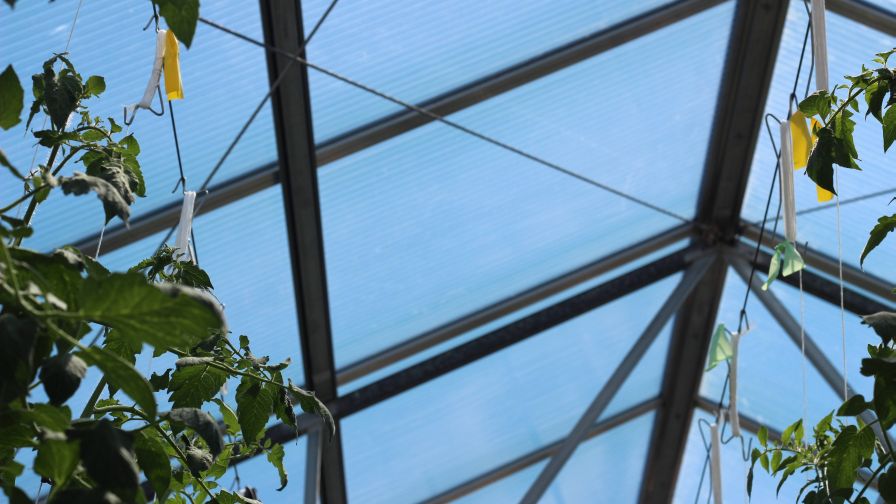
This glazing photo shows the lyris heat-blocking greenhouse roof, as described below in the “Spectral Glazing” section. Photo: Nadia Sabeh/Red Sea Farms
Depending on the climate, the crop, and the market, conventional greenhouse climate management systems, such as boilers, evaporative cooling pads, and exhaust fans, may not provide the level of control necessary to grow a consistent product year-round.
The following is a list of six major trends we’re seeing in the greenhouse industry as they relate to heating, ventilation, and air conditioning (HVAC) and environmental management, especially in the wake of higher energy costs and increased regulations.
Spectral Glazing
There are a lot of cool new glazing options hitting the market that could make a big impact on the heating and cooling needs of the greenhouse. There are new spectrum-blocking glazings that block near infrared (NIR) wavelengths, effectively lowering the amount of solar heat gain into the greenhouse and reducing cooling needs. There are also new spectrum-modifying glazings that shift the high-energy ultraviolet and blue wavelengths into lower-energy yellow and red wavelengths that are more photosynthetically active. And then there are electricity-producing glazings that have thin strips of solar panels embedded into the glass cover, while converting green into red light. All of these new glazing options have the potential to reduce energy use and costs associated with cooling and heating the greenhouse.
Mechanical Cooling and Dehumidification
In humid climates where ventilation and evaporative cooling don’t work so well, mechanical cooling (aka, air conditioning) and dehumidification is becoming a more viable, and potentially sole, solution to managing the greenhouse environment and selling consistent product year-round. Ideally, these systems would be operated in a sealed greenhouse, where only the interior air is being conditioned, not the outside air before it is brought in. However, it’s very difficult to keep the sun out, especially since access to sunlight is precisely why many growers choose a greenhouse over an indoor facility. This heat from solar radiation is immense. Combine that with the greenhouse effect created by the glazing and suddenly it becomes apparent that you will need a lot of air conditioning. When comparing a 10,000-square-foot greenhouse and a 10,000-square-foot warehouse with high-pressure sodium lighting spaced in a 5×5 grid pattern, the indoor facility requires about 115 tons of cooling and the greenhouse requires 170 tons. That’s almost 50% more air conditioning required for the greenhouse. Not only is air conditioning energy intensive (e.g., high operating costs), the equipment itself is expensive, typically more than $3,000 per ton.
Heat Pump Heating
As states like California eye electrification and decarbonization to limit or reduce global warming and climate variability, gas-fired greenhouse heating systems, such as boilers and unit heaters, may become a thing of the past. Electric heat pumps are likely to become their replacement. Heat pumps essentially work by sucking up heat from one location and then pumping it somewhere else. This action basically makes them reversible: on a cold day they can suck heat from the outside surrounding and pump it into the greenhouse, and on a hot day they can suck the heat out of the greenhouse and pump it outside. Heat pumps can use heat from the outside air, the ground, a water source, or even a geothermal vent or pool, making them incredibly versatile. In general, air-source heat pumps are more effective in mild climates and ground-source heat pumps are most effective when there is a balanced need for heating and cooling on a daily or annual basis.
Sealed or Hybrid Greenhouse
More frequently, we’re seeing greenhouses built to recirculate or push outside air in (positive pressure), rather than suck air out with big exhaust fans (negative pressure). Greenhouses that only recirculate air are “sealed” greenhouses, whereas those that might use a combination of recirculating and outside air are called “hybrid” greenhouses. The trend toward this style of greenhouse is associated with having more precise management of temperature and humidity, better containment of carbon dioxide and odors (for cannabis), better control of pests and air quality, and improved air uniformity. These greenhouses are typically built with an ante-chamber, where the air is preconditioned using heaters, evaporative cooling, air conditioning, or other systems and then pushed into the greenhouse through air tubes or blower fans. The downside to these systems is the need for more sophisticated and expensive monitoring and controls, as well as initial and ongoing air balancing to ensure adequate delivery and mixing of conditioned air and to prevent over-pressurization of the greenhouse structure.
Canopy-Direct Air Movement
Moving air in and around the plants can help manage leaf temperature and canopy humidity. Ceiling fans can be an effective method for directing air downward into the head, facilitating evapotranspiration and helping to prevent leaf tip burn. Under-canopy air distribution using inflatable tubes, fabric ducts, or metal ducts is becoming more popular for tall canopy crops, such as tomatoes and cannabis. This under-canopy air movement helps to break up pockets of humidity and reduces temperature stratification. Heated or cooled air is pushed through the tubes and ducts using fans, usually located at one end of the greenhouse. If plants are elevated on a bench or table, it’s important that the top is open-lattice to allow air to flow through it.
California’s New Energy Code
Effective Jan. 1, 2023, new greenhouses built in California need to comply with a set of mandatory measures aimed at reducing energy consumption, regardless of the crop being grown. If the greenhouse will be heated and cooled, the envelope will need to have at least two layers of glazing, separated by air, argon, or other insulating gas. Double inflated polyethylene, twin wall polycarbonate and acrylic, and double or triple-pane glass will meet the code requirement. Heating and mechanical cooling systems will also need to meet the minimum efficiency requirements spelled out in the CA Mechanical Code based on their type and size. In case you’re wondering, and I’m sure you are, there are requirements for lighting as well. All new horticultural lighting is to have a minimum PPF of 1.9 umol/Joule and be aggregated at the electrical panel for possible and future submetering. If you want to learn more about what’s in and what’s not in the new code, check out my February 2023 blog posted on our website.
Although conventional greenhouse climate management systems are still very popular and cost-effective strategies for managing temperature and humidity, they are no longer the only option. For growers who want (or need) to produce a consistent crop year-round, managing the greenhouse environment is becoming more precision-control oriented. It’s also becoming a necessity for growers who want to feed the world or their local communities in challenging climates. The development and implementation of new systems that provide further protection from the outside, reduce the industry’s carbon footprint, and create the climate that plants crave is encouraging for the longevity of the greenhouse industry.