Why Now Is the Time to Switch to High-Efficiency Lighting
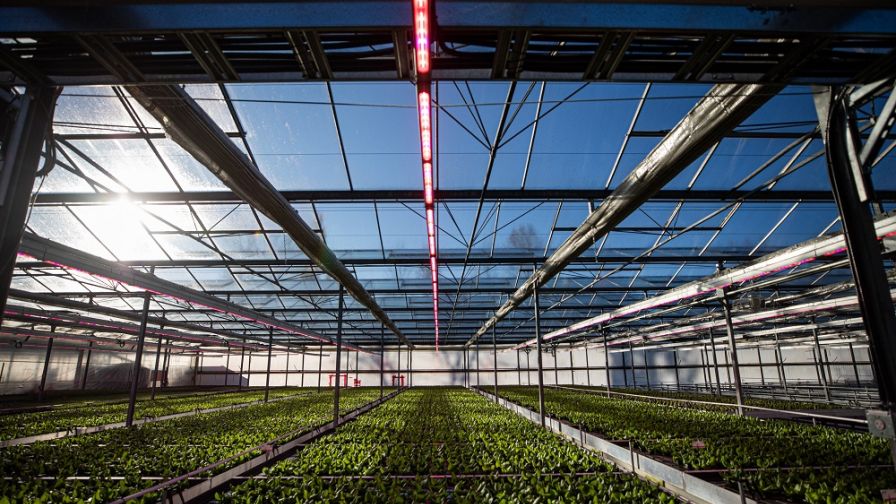
Photo: Resource Innovation Institute
For years, Resource Innovation Institute (RII) has preached the energy efficiency and productivity benefits of light-emitting diode (LED) fixtures. We’ve worked with industry partners, utilities, and policymakers to identify best practices for controlled environment agriculture (CEA) and increase the adoption rate of these efficient lighting systems. That work has paid off, as more and more operations continue to adopt LED lighting fixtures for their greenhouse and/or indoor CEA operations.
Now equipped with real-world data and use cases, regulators are developing regulations, standards, and technical requirements that will essentially mandate the use of high-efficiency systems. This means there is no better time for operations still using legacy lighting systems to make the LED leap.
Why LEDs?
CEA operations often operate on tight margins. The cannabis cultivation competition is “cutthroat,” says RII member Thomas Lor, an Engineering & Design Solutions Engineer at Southern California Edison. As a representative of the power utility, he works with many cannabis operations in southern California in developing energy load management plans.
“Compared to 2018, their profit margins have contracted an incredible amount and are continuing to see downward pressure in the face of increasing costs and competition,” he shares. “Now that the initial market boom has kind of subsided, savvier operators are realizing that process efficiencies need to be maximized for a lot of these businesses to remain viable.” He notes that energy bills make up a significant portion of total operating costs, and “doing something as simple as moving to LED lighting technology can help slash your energy bill by 30 to 40%.”
LED maintenance costs are also generally less than their high-intensity discharge (HID) counterparts, “usually limited to cleaning the lenses or lens covers per the manufacturer’s instructions and specific to conditions in the growing environment,” RII member Neil Coppinger, Key Account Manager – Horticulture LED Solutions at Signify, says. “Growers will want to make sure chemical film and dust are removed annually so light output is maximized.”
Beyond efficiency, advancements in LEDs have increased these systems’ efficacy.
“Some lighting control systems allow growers to set crop-specific light recipes supported by a micro scheduling capability. The result is the right light is delivered in the most efficient manner throughout the production cycle of any given crop,” Coppinger says. Even in greenhouse environments, LEDs can be fine-tuned to balance production and efficiency. “Growers are also able to dial in specific daily light requirements and adjust as day-to-day climate changes, such as cloudy vs. sunny days,” Coppinger adds.
Dimmibality is a feature that regulators and standards providers increasingly are turning to. For example, the DesignLights Consortium (DLC), a non-profit organization that works on lighting solutions to reduce energy use, carbon, and light pollution, requires dimming ability for all but the lower-light output product in its newest technical requirements, explains Leora Radetsky, Senior Lighting Scientist at RII member DLC.
“We believe that there’s a great value for dimming not only for energy and cost savings, but also for the plant to be able to better respond to its environment,” Radetsky says. “You can use dimming along with other factors in order to optimize the environment. We think that’s important because these products are installed for a long time. We’re not just talking about for a season or two – they might be there for 10 or 15 years, and the benefit of dimming and spectral tuning is it also allows the grower to potentially grow more crops, and future-proof your facility,” she adds.
Carrots and Sticks
As mentioned, many CEA operations have already made the switch to high-efficiency lighting systems, often with help from utility incentive programs. But as baseline efficiency increases, incentive programs will be wound down, meaning the clock is ticking to maximize the rebate and incentive value for adopting these technologies.
“For new builds and retrofits, some states are beginning to mandate LEDs and eliminating HID lighting as an option. As a result, rebate programs are being scaled back or phased out altogether,” Coppinger says.
For SCE specifically, Lor says the LED light incentive programs remain, but does note that the baseline against which energy efficiency gains are measured has become more stringent.
“Incentive dollar amounts are typically based on the difference between the calculated annual energy usage of the more efficient technology and that of the less efficient legacy lighting,” he explains.
That legacy lighting used to be single-ended high-pressure sodium (HPS) fixtures, but a recent California energy code change has established a minimum efficacy requirement that all but mandates the use of double-ended HPS fixtures or better. All else equal, this has led to decreased incentive amounts for CEA operations. Lor estimates we are “just past maximum achievable incentives for lighting measures.”
New proposed energy code standards would further increase the minimum efficiency threshold for California CEA operators. In its latest proposal, California’s Statewide CASE Team aims “to increase the minimum PPE for luminaires and lamps used to grow plants in indoor facilities from 1.9 to an LED based efficacy, at least 2.3 µmol/J. This change would mandate the use of LEDs whereas HPS lamps can meet the existing requirements.”
Not all standards or technical requirements are sticks meant to enforce compliance. Some, like those used to evaluate products on DLC’s Qualified Product List (QPL), have been developed to make purchasing decisions easier.
“We have measurement requirements for PPF, PPE, and spectrum from the IES and ASABE and those are deeply embedded into the DLC technical requirements,” Radetsky says. “Products that meet those requirements are on the QPL. And one of the benefits of the QPL is that you will see a graph of the spectral quantum distribution, so you can actually see what the spectrum is. You can see what the shape of the beam is with a graph of the photosynthetic photon intensity distribution, so you can actually learn a little bit about the product.” Many utilities then use the DLC’s QPL to offer rebates, she adds.
Transition Tips
Making the switch to LED lights is not as simple as swapping fixtures and turning on the power. For example, “in colder months, HID lights do contribute to overall heat in the greenhouse,” Coppinger says. That heat load loss “must be accounted for in the new LED environment as they produce less radiant heat. For those customers that also light in warmer months, LEDs can have a significant energy reduction impact over HID by reducing the required cooling load,” he continues.
He also advises operations looking to have lighting installed and operational by the beginning of the North American lighting season “need to work with their suppliers to get light plans developed, installation and project details formalized, and orders placed by mid-summer.”
While growers should expect their lighting vendor to help them calculate and understand expected production for the planned growing environment, Radetsky advises growers consider interoperability in their purchasing decision.
“We have seen cases where a specific manufacturer and control type is installed in a greenhouse, and unfortunately that [controls] business goes out of business, and then essentially that controller is no longer functional.”
With non-functioning controls, lighting fixtures lose their functionality.
“Interoperability allows you to future-proof your products. That’s something that we are really interested in for the long-term viability and cost-effectiveness of CEA,” Radetsky explains.
When looking for utility incentive programs, Lor says the most important thing CEA operations need to do is to contact their utility as early as possible in the decision-making process. “Program rules can vary widely across utilities,” he says. For example, some incentive programs might allow for engineering planning costs to be included in the incentive project, but others may not.
“It’s really important to talk to the utility ahead of time to understand these nuanced rules,” Lor stresses. “Most energy efficiency programs for new construction require the utility to demonstrate that incentives would meaningfully influence the adoption of more efficient technology. This cannot be done retroactively. There are times when customers engage us about a project for the first time and inform us that they’ve locked in their design and ordered their equipment. ‘Here’s everything I’m putting in. How much can I get?’ That unfortunately becomes $100,000 to $300,000 of potential incentives that they are no longer eligible for because that conversation did not happen a few months earlier.”
With advancements in LEDs and their controls increasingly becoming the focus of academic research, they also present a solution to operational and business challenges. They are actively used in commercial settings, and their real-world results are prompting regulatory enforcement. Making the LED leap sooner than later will not only help businesses maximize utility incentives and rebates while they remain available but also position them for long-term success by reducing operational costs and maximizing crop growth.
As Radetsky says, the tunability of LED fixtures “will allow us to do more with less, which is something that we all want to do.”