2023 Plug and Liner Survey: How Growers Are Dealing With Shipping, Energy, and Other Challenges
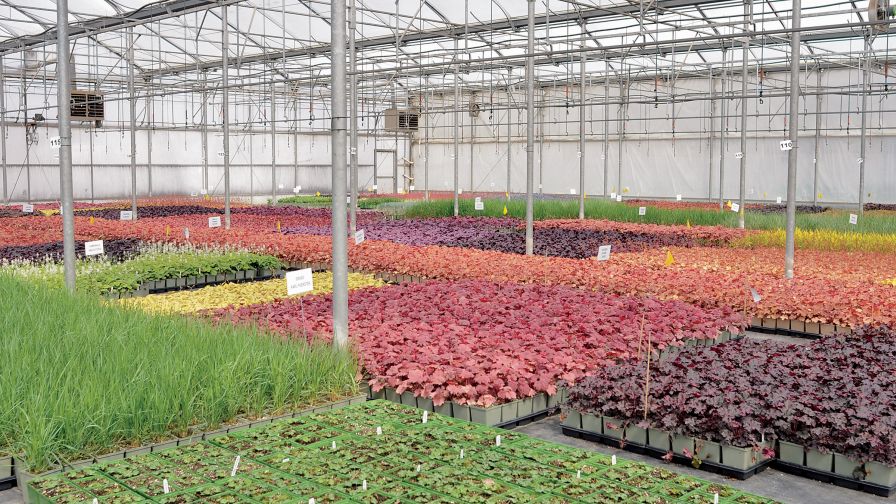
Photo: Greenhouse Grower
Young plant growers tend to deal with many of the same challenges as their customers. Because they are further up the supply chain, their response to these challenges can be critical. After all, if plants are delivered late, or arrive with subpar quality, the ripple effect can be huge.
Greenhouse Grower’s 2023 Plug and Liner survey focused on some of these major challenges, and the strategies growers follow to deal with them. One of these challenges is shipping. Among the 50-plus growers of all sizes who completed this year’s survey, most say the biggest shipping issue is rising costs.
“Freight costs have increased since the pandemic started, and we and our customers have had to make do,” said one respondent. “Some customers have consolidated suppliers to reduce freight costs or have selected suppliers located closer to them rather than farther across the country.”
Most respondents said they have to pass these costs along to their customers.
“Our plug costs do not include shipping costs,” said another respondent. “Shipping costs are added at the time of shipping.”
The good news is there are ways to alleviate some of these costs:
- “We offer attractive truck freight pricing so long as total dollar order minimums are hit, which encourages both full trucks as well as full racks.”
- “We do a lot of zone skipping, meaning we drop at major hubs in Memphis, Columbus, Newark, and Boston to help keep shipping costs lower and keep the product in our control longer. We have switched a lot of business from FedEx to UPS; we found UPS to be less expensive, fewer delays, and 60% fewer damage claims.”
- “We look to combine orders so all ship on the same week.”
When it comes to energy, young plant growers often have to absorb winter energy costs for their finished grower customers. In this year’s survey, we also asked what you are doing to conserve energy and cope with heating costs. Here are some of the top responses:
- “Our heating energy is supplied by recycled woodchips, which was a significant investment when put in but has paid off greatly over time.”
- “We condensed our operation to reduce square footage used for early plugs.”
- “Buying fuel on contracts to lock down cost, reducing temperatures 2 to 4 degrees when possible.”
- “We have installed bottom heat in our entire facility and heat curtains. All of our boilers are equipped with high efficiency burners and use mostly natural gas.”
- “We have added heat retention curtains and are now changing to more efficient boilers. We moved our entire propagation area so that we can reduce traffic through that part of the greenhouse and installed a true humidification system.”
What is your biggest challenge as a young plant grower and how are you solving it?
- “Reaching as close to 100% on-time and in-full order fulfillment as possible. Reducing our program item list is one way we are working to achieve this. There are so many equivalent plants out there from the various breeders that having duplicate production jobs introduces the possibility for errors that affect yield.”
- “Old Greenhouses. Looking to convert new booms to growing areas. Automation for transplanting or sticking, or reworking plug trays.”
- “Supply of tissue culture and unrooted cuttings are some of the biggest challenges. We mitigate this by ordering early and staying in communication with our vendors.”
- “Labor has been an ongoing issue and we have now gone to supplying part of our labor force with H-2A workers.”
- “We continue to hire and train very unskilled workers in our growing department.”
- “Since we developed our own computer software, we are constantly writing new code to make shipping the plugs more efficient.”
- “To be in this business, a basic level of quality is required. The next level of quality is harder to define and promote. We have improved our quality check process, so we are able to notify customers earlier when there are shortages or extras. We all have the same genetics, so it often just comes down to logistics. We have set truck delivery schedules and combine orders to best utilize truck options.”